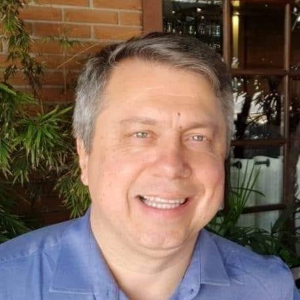
Muitas empresas buscam conquistar novos clientes, novos negócios, aumentar o volume de vendas e faturamento, para obter um melhor resultado, e se esquecem de que também é importante eliminar, ou ao menos minimizar, as perdas.
A perda não agrega valor ao cliente ou à empresa. Os clientes não estão dispostos a pagar por ela.
Somente aquilo que modifica o produto ou torna o serviço de maior qualidade, mais rápido, confiável, é que agrega valor.
Uma forma de sensibilizar as pessoas quanto à importância da perda, e a necessidade de eliminá-la, é calcular os custos/despesas envolvidos no período de 12 meses e pensar sobre o que poderia ser feito com o dinheiro, se estivesse disponível.
O Sistema Toyota de Produção, baseado nos princípios do Pensamento Enxuto (Lean Thinking), apresenta as 7 grandes perdas:
- Estoques
A empresa que estoca produtos acabados ou semiacabados, por exemplo, acaba escondendo boa parte da sua ineficiência, baixa produtividade, não conformidades nas etapas da produção.
Quando a empresa minimiza ou elimina estoques, a falha em uma máquina ou equipamento se torna evidente, o atraso na entrega por um fornecedor se torna notório e com isto, ações devem ser tomadas, prontamente, para se melhorar o desempenho.
Estoques: custam e mobilizam capital de giro; requerem recursos (espaço, pessoal); ocorrerem perdas devido à deterioração de produtos estocados e à obsolescência.
A produção em pequenos lotes e conforme pedido confirmado (e não baseada em previsão) pode reduzir os estoques.
- Esperas
As esperas podem estar relacionadas aos gargalos, que existem por falta de um balanceamento (equilíbrio) entre recursos.
No dia a dia das empresas, não é raro vermos duas ou três pessoas, aguardando, para falar com o responsável da área e/ou para obter uma aprovação, assinatura em um documento. É interessante se questionar a real necessidade de algumas assinaturas, ou liberações.
Layouts dedicados por tipo de operação exigem o transporte entre áreas. É comum, ainda, que uma operação se inicie somente ao término da anterior. Nestas duas situações, podem ocorrer esperas. Uma solução seria o uso combinado de pequenos lotes e de células de manufatura (em U, em W).
- Transporte
O único segmento que deve gostar de transporte é o logístico. Em outros ramos, o transporte não agrega valor.
Para haver a minimização do transporte de materiais, deve-se repensar a disposição dos recursos da empresa (layout).
Em operações de manufatura, o uso de células de manufatura (em U, em W) pode minimizar os transportes entre operações, quando comparado com os layouts por operações, onde se tem uma área de corte, outra de usinagem, outra de laminação, etc..
- Fabricação de produtos com defeito, execução de atividades/serviços incompletos/errados
O “fazer certo da primeira vez” seria o melhor dos mundos. Mas, no dia a dia, descobrem-se produtos e atividades fora da especificação e inadequados ao uso pretendido. É um balde de água fria, e em geral, o ambiente fica ruim.
Resta: retrabalhar (quando possível), o que acaba incorrendo em gastos não previstos e atraso na entrega do produto/serviço; reclassificar o produto, para uma classe inferior; negociar com o cliente um desconto, para aceite pelo mesmo, como está (ou ainda após o retrabalho); refugar/descartar o produto, vendendo, quando possível, como sucata/resíduo.
Atividades e serviços incompletos, inadequados, errados: quantas vezes, recebemos um relatório, ou um documento (pedido de compra, nota fiscal), que não estava correto, e que precisou ser corrigido mais de uma vez?
Os erros podem ser minimizados, através do uso de checklists (listas de verificação), que são duplamente utilizadas num voo comercial, apesar da qualificação dos pilotos e de sistema à prova de erro (fool proof ) – utilizado, por exemplo, no chip do celular, que possui um chanfro, que só permite a montagem na posição correta.
- Desperdício de movimentos
A ergonomia estuda como adequar o posto de trabalho ao funcionário, e não o contrário.
Algumas observações são bastante intuitivas: giros desnecessários do corpo, distâncias percorridas, que poderiam ser evitados.
Vale a pena contratar um especialista, para realizar um laudo ergonômico, com o objetivo de melhorar os movimentos das pessoas, durante a execução das atividades.
- Superprodução
Significa: produzir antes do que o necessário e/ou produzir quantidade maior do que a necessária.
Resulta em utilizar recursos (mão de obra, máquina/equipamento, espaço), que poderiam ser utilizados para produzir outro produto mais necessário. Acabam gerando estoque (perda já abordada).
Uma forma de minimizar o problema é trabalhar de acordo com pedidos confirmados (e não baseando-se em previsões) e utilizar pequenos lotes, que são possíveis com a redução do tempo de preparação (setup).
- Processamento
Etapas do processo pouco produtivas ou desnecessárias, em função de atributos não exigidos pelo cliente, mas que se deu importância, internamente, na empresa, e não se sabe o porquê.
Meios para se minimizar esta perda:
- análise crítica do que está sendo feito x o que deve ser feito, em termos de características do produto, na ótica do cliente; eliminação de atributos e de operações desnecessárias;
- melhorias nas operações, através da otimização de movimentos, aproximações dos recursos utilizados;
- setup rápido, proporcionando maior disponibilidade, pois a máquina/equipamento fica menos tempo parado, sem processamento; com isto, aumenta a capacidade de produção. É importante lembrar que atividades de inspeção, embalagem também requerem preparação (setup).
Em uma empresa, a inicialização do computador da faturista levava 10 minutos – até ser finalmente corrigido o problema.
Aprender a enxergar
O grande desafio é o de enxergar estas situações desfavoráveis e, claro, ter a disposição para corrigi-las. Quando os problemas são muito óbvios, não existe dificuldade em detectá-los. Porém, com o tempo, após a solução dos mais visíveis, os restantes podem estar mais escondidos e necessitamos de métodos para identificá-los.
Nos próximos artigos, vamos apresentar: fontes de informação e métodos para identificação de oportunidades e implantação da melhoria contínua, através dos Kaizens.
Sobre o Autor:
Ronaldo de Fávero, consultor em gestão empresarial desde 1992
e-Mail: ronaldo.favero@terra.com.br
Celular / WhatsApp: (11) 95163-1030